2016 ISPE Europe Conference on Biotechnology

Reinventing Commercial Biomanufacturing Frankfurt, Germany 24–25 October 2016
One hundred fifty attendees met in Frankfurt at Sanofi’s wonderfully restored historic building “Alte Färberei,” where the Farbwerke Höchst Corporation manufactured fabric dyes a century ago.
With a strong scientific program, exceptional speakers, important regulatory updates, and stimulating presentations, the scene was set for excellent networking opportunities and friendly debate, as well as solutions for and conclusions on the current issues facing the biotechnology field.
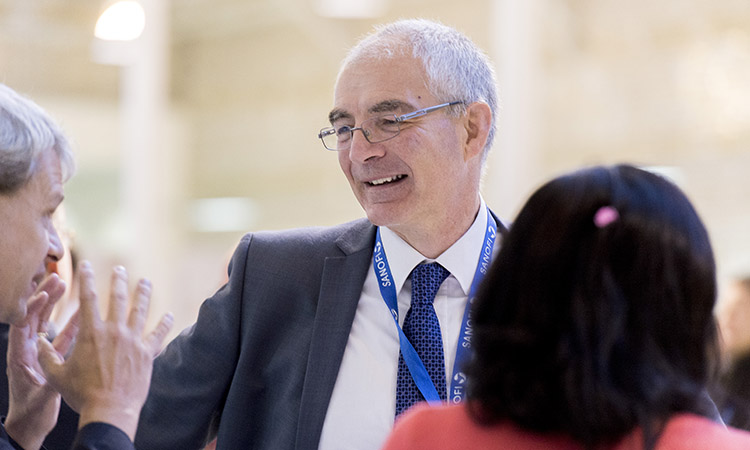
Day 1
Andrew Hopkins, an MHRA GMP Inspector and Chair of the joint EMA and PIC/S working group on the EU GMP Annex 1 update, opened the Quality and Regulatory Session. He discussed the agency’s new Innovation Office, established in 2012 to provide a single point of access to expert regulatory information, advice, and guidance to help organizations of all backgrounds and sizes develop innovative medicines, new medical devices, or novel manufacturing processes.
Hopkins encouraged industry members to contact to the office with their questions. Hopkins noted that processes are often not well defined in biologics, a situation that may lead to difficult inspections. In the future, he explained, inspections might be additionally affected by the new “Good Manufacturing Practice for Advanced Therapy Medicinal Products” guidance produced by the European Commission and EMA, which is currently in the public commenting period.
Kavita Ramalingam lyer, a regulatory professional from Merck Sharp & Dohme Corp., highlighted the influence of Annexes 1 and 2 on biologicals manufacturing. As a Biophorum benchmark study revealed inconsistent room and area classifications, she encouraged attendees to do “proportionate quality risk management” to better support risk assessments with data. In addition, she continued, clarified guidance in Annex 2 would be helpful.
Jörgen Magnus, Research and Development Manager from Bayer Technology Services, demonstrated a model for batch definition and out-of-specification investigation in a continuous biological process.
Leif Poulsen, Global Technology Partner, Automation and IT, NNE Pharmaplan, opened the Knowledge Management session, explaining how to organize knowledge management in a big corporation. He highlighted communities of interest (COIs), ensuring a common language, standardizing processes, and striving for consistent, high-quality solutions. Management bodies in the model are a COI board, competency board, human resources board, quality manufacturing board, and resource management in the whole network.
Ciaran Kelleher, Senior Process Engineer, Janssen Biologics, Ireland, described a systematic cross-disciplinary approach to tech-transfer projects based on the ISPE Technology Transfer Good Practice Guide. He demonstrated a range of smart tools for sharing knowledge and experience throughout a tech-transfer project, part of a wiki-like process from development to chemistry, manufacturing, and controls and commercial manufacturing.
This interesting afternoon ended with a presentation by Elena Galiana Jaime, Senior Knowledge Manager, BASF, which demonstrated knowledge-transfer methods and tools in the global BASF community.
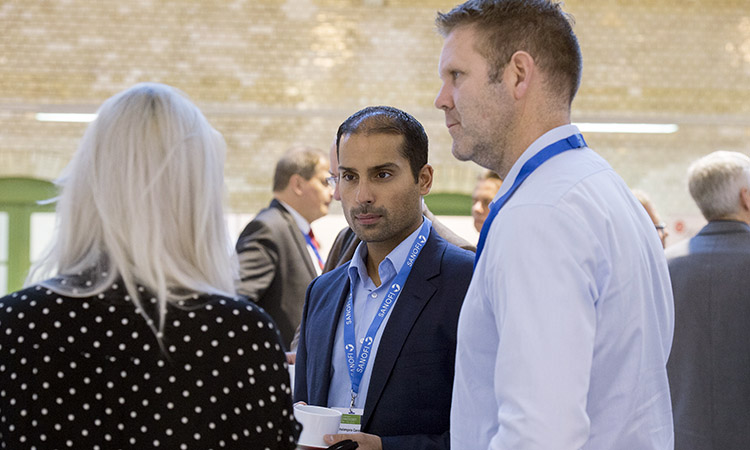
Day 2
Tuesday began with “Data Science as Enabler for Scale-Up, Technology Transfer, and Root Cause Analysis in Manufacturing,” presented by Stefan Krahulec, Senior Manager Technology and Innovation, and Georg Klima, Executive Director Process Science Austria, both of Boehringer Ingelheim, Vienna. Their session focused on three case studies from biopharmaceutical operations: root cause analysis, chromatography, and automation.
Next, Safaraz Niazi, Chair and Chief Science Officer of Therapeutic Proteins International, discussed the company’s improvements to the biomanufacturing process: combining the fermentation and recovery steps to reduce the number of tanks and eliminate centrifuges, harnessing the power of gravity to diminish the need for pumps, and placing placed single-use bags horizontally to reduce the fluid level and obviate the stirrer.
Dr Imre Molnar, Molnar Institut, Berlin, presented a way to shorten biologicals’ time to market using computer-based data modeling. This new technology leads to much better understanding of the analytical process and variabilities affected by the analytical setup, and facilitates communication between applicants and regulators in the product dossier reviewing process. Experiments can be done in seconds; design spaces are visualized in three dimensions, and can be combined with additional components in the analytical process.
The technology and innovation session featured new concepts for all areas of biologics manufacturing: upstream and downstream processing, followed by fill and finish.
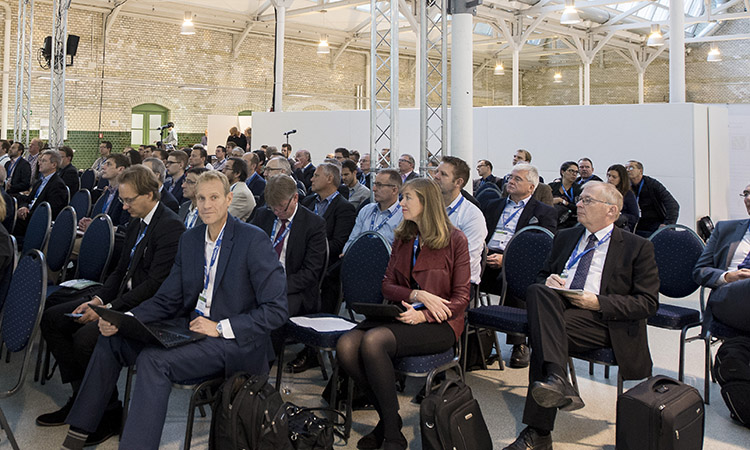
Digitalization will result in much more automation and biologicals manufacturing, said Christian Woelbeling, Senior Director, Global Accounts, Werum Corporation. He previewed an industry-4.0-based production control strategy as a holistic and overarching concept, explaining how the production control strategy would fit into the existing concepts of quality by design, critical process parameters, critical quality attributes, and more.
“Construction and Qualification of a Large-Scale Microbial Manufacturing Plant” was presented by Jean-Luc Roulin, Head of Bio Drug Substance Operations, UCB. He demonstrated the “Edelweiss Project” case study—fast-track design and construction of a large-scale microbial plant for CIMZIA (certolizumab pegol). At its peak, 600 people worked on this project; implementation was done within 30 months. The project strategy was modularization of engineering and construction. Key elements were utilities and distribution, packaging strategy procurement, parallel execution, and integrated on-site installation. The second step was lean qualification using verification and risk-based approaches designed to foster process understanding and focus on critical points, subject matter expert empowerment, and reduced workload.
Britt Petty, Director of Biologics Manufacturing Operations, Biogen, discussed “Preparing Manufacturing Capabilities for Breakthrough Therapies.” He explained the technological goals for upstream and downstream processing in building a large-scale biologics manufacturing plant. Focus on upstream processing will help produce more drug substance more quickly while reducing bottlenecks in N-1 perfusion and higher titers in bioreactors. Focus on downstream processing will purify more drug substance by handling higher titers with high-capacity resin, single-pass tangential flow filtration, and buffer concentrates.
“Single-Use Depth Filter with Hyperion Flow: No Centrifuge Requirement in Mammalian Cell Culture Harvesting Applications up to 2000L” was presented by Silke Bergheim-Pietza, Marketing Manager, Pall Life Sciences Corporation.
“Innovations in Fill and Finish Processes” were shown by Frank Lehle, Site Manager, Vetter Pharma Corporation. The company technology standard V-CRT@, Vetter Clean Room Technology, is focused on a sophisticated combination of isolators and restricted-access barrier system (RABS) technology. Industry trends such as a continuous change of products, smaller products, orphan drugs, and ophthalmic drugs have led to increased flexibility requirements. Other timely topics are quality requirements such as “essentially free from particles” to “practically free from particles” and zero colony forming units in RABS and isolators. A fully automated peroxide decontamination is part of this best practice approach. This very-well-thought-through production concept shows how to “improve quality—keep overall equipment effectiveness and flexibility.”
All presentations were followed by interactive panel discussions that allowed the audience engage the speakers in lively question-and-answer sessions.