Pharma Facilities & Equipment: Heat Recovery Regulations & HVAC Energy Consumption

Regulatory codes that require exhaust-air heat recovery on heating, ventilation, and air-conditioning (HVAC) systems have a significant impact on construction, maintenance, and energy costs. Ideally, they should reduce energy consumption and diminish a facility’s carbon footprint. These are good intentions, but what if the regulations have the opposite effect?
This article compares the performance of standard systems and alternative approaches and shows that code-compliant air-handling systems can increase energy consumption.
Background
This article was derived from the authors’ experiences with three projects: two in Ireland that required compliance with European Union (EU) exhaust-heat-recovery regulations and one in Switzerland with nearly identical mandates.
The current EU exhaust-air energy-recovery requirement is outlined in the Ecodesign Directive 2009, Regulation 1253/2014,1 which mandates exhaust-air-heat-recovery systems for air-handling units (AHUs) with 10% or more outdoor air (OA). Heat-recovery effectiveness (efficiency) specifications range from 68% to 73%, depending on heat-recovery type.
The regulation provides exceptions for a limited number of applications, such as:
- High occupant risk if fresh OA could be contaminated by toxic exhaust (e.g., explosive, toxic, corrosive, or flammable environments)
- Systems for emergency use only (smoke purge, etc.)
- Areas with high internal heat loads (such as electrical and computer rooms where heat recovery adds no benefit)
In Ireland, AHUs that serve pharmaceutical cleanrooms fall within the scope of the regulation because these spaces are designed to accommodate routine and frequent human occupancy. Mechanical utility spaces also fall within the regulation for the same reason.
Switzerland has its own standard: SIA 548 282/2.2 Section 5.10.3 says that any AHU with more than 10% OA requires exhaust heat recovery that is 70% effective on sensible load. There is no option to avoid the requirement by using another means of heat recovery.
In the United States, the ASHRAE 90.13 standard provides the minimum requirements for energy-efficient design of most commercial buildings. The standard varies by climate zone and by version,∗ but typically re quires exhaust-air heat recovery that is 50% effective for systems with 10% or more OA. Unlike the EU and Swiss regulations, the US standard also factors heat recovered from other sources to minimize exhaust heat recovery requirements.
Each regulation allows the designer to determine the type of heat recovery used to transfer heat between the exhaust air stream and the fresh outdoor airstream, such as:
- Enthalpy wheel—rotation transfers both heat and moisture between two side-by-side airstreams
- Heat pipe—a sealed pipe with refrigerant that transfers heat between side-by-side airstreams
- Air-to-air heat exchanger—typically a plate-and-frame heat exchanger that transfers heat between two side-by-side airstreams
- Run-around loop—a system that pumps heat-transfer fluid between two heat exchangers, one in the outdoor airstream and the other in the exhaust
Heat-recovery equipment, its associated ductwork, and the additional building volume required for side-by-side airstreams add considerable cost to facility design. While run-around loop systems need not be side by side, meeting the heat-transfer effectiveness dictated by US, EU, and Swiss regulations requires both outdoor and exhaust air coils with significant depth, with associated air-side coil pressure drop and fan energy.
The projects considered in this analysis use the lower-cost run-around loop; the end result, however, will be affected only by capital cost. The air-handling systems presented here are always in cooling mode at lower OA rates, so heat recovery is not beneficial, regardless of the type used.
Analysis
OA rates for pharmaceutical manufacturing clean and utility spaces typically range between 5% and 15%. Cleanroom air change rates are high and drive small temperature differentials between supply air and room set points. Mixing return air with OA at 5%–15% at design winter conditions is more likely to lead to a cooling load rather than a heating load, making heat recovery on these systems ineffective. Air-handling systems with low air-change rates—such as those for mechanical utility spaces—do not benefit from exhaust-air heat recovery either. These areas have equipment that emits enough heat to eliminate the need for heating throughout the year.
To provide a wide range of climate zones for this analysis, four European locations were considered: 1) Wynau, Switzerland, 2) Dublin, Ireland, 3) Helsinki, Finland, and 4) Athens, Greece. All were reviewed against the schematic shown in Figure 1.
*There is a new version every three years, and different cities require compliance to different versions.
This paper reviews four system options, all of which use a fixed volume of supply air:
- Standard air-handling system with no heat recovery
- Run-around loop heat recovery with an air-side bypass, which reduces energy consumption by allowing the air to bypass heat-recovery equipment when not needed
- Run-around loop heat recovery without an air-side bypass
- Standard air-handling system with an air-side economizer for free cooling
- 1Eur-Lex. “Commission Regulation (EU) No 1253/2014 of 7 July 2014 Implementing Directive 2009/125/EC of the European Parliament and of the Council with Regard to Ecodesign Requirements for Ventilation Units.” 7 July 2014. http://eur-lex.europa.eu/legal-content/EN/ TXT/?uri=uriserv:OJ.L_.2014.337.01.0008.01.ENG
- 2SIA. Standard 382/1. Lüftungs-und Klimaanlagen—Allgemeine Grundlagen und Anforderungen. http://shop.sia.ch/normenwerk/architekt/382-1_2014_d/D/Product
- 3AHSRAE. Standard 90.1–2016: “Energy Standard for Buildings Except Low-Rise Residential Buildings.”
Standard system
The standard system is based on a primary air handler that mixes required OA and return air and conditions the airstream to meet room loads. In summer, when outdoor humidity is high, the system operates in dehumidification mode, passing the airstream through a cooling coil to drop the temperature to condense moisture out of the airstream. When both OA temperature and humidity are high, the system overcools the airstream, then passes it through a reheat coil to maintain both humidity and temperature within specified limits. Reheating is usually not needed in cold weather.
Run-around loop
An air-handling system with a run-around loop has a glycol coil loop and two heat exchangers, one in the outdoor airstream and the other in the exhaust. The glycol is pumped to precool the outdoor airstream in summer, and to add heat in winter. As mentioned above, heating is normally needed only in summer to provide reheat after the cooling coil. Heat recovery only helps to reduce summer cooling load. To meet regulations, however, the system requires deep coils to provide the required heat-exchanger capacity. This increases fan and pump energy consumption, which o sets energy savings of preconditioning the OA.
Regulations also require the ability to turn o heat recovery. This can be done in two ways:
- Shutting down the pump: This incurs the lowest capital cost, but it increases fan energy consumption by requiring that the fan push air through the coils 24/7.
- Bypass around the coils: This has a higher capital cost and requires more space, but reduces fan energy consumption when the system is o and the air can bypass the heat-recovery coils.
Figure 1 Location | Temperatures °C | Description | ||
---|---|---|---|---|
Clean Description Space |
Utility Space |
|||
1 | 21.2 | 22.9 | Summer: no heat recovery | |
19.2 | 19.9 | winter: no heat recovery | ||
2 | 12.3 | 12.3 | Summer: cooling | |
16.8 | 15.6 | Winter: cooling | ||
3 | 16.8 | 13.4–15.6 | Utility: | 13.4°C summer |
15.6°C winter | ||||
4 | 18.2 | 14.5–16.5 | Utility: | 14.5°C summer |
16.5°C winter | ||||
5 | 20.0 | 22.0 | ||
6 | 20.8 | 22.7 | ||
Outdoor air: summer 25°C; winter –5°C |
Air-side economizer
An air-side economizer is not a heat-recovery device: It is a heat-relief device. Since year-round cooling is normally required for low-percentage OA handling systems, an air-side economizer takes advantage of lower OA temperatures/energy levels when conditions allow. When the OA temperature is below the return air temperature and outdoor air humidity is low, the economizer modulates the outdoor and exhaust/relief airflows to meet the space set point temperature while minimizing the cooling load.
Since this is not heat-recovery equipment, however, it does not meet the heat-recovery requirements outlined by regulations. It is, however, a much better alternative to lower energy consumption.
For one project in Ireland, the owner wanted to install air-side economizers to reduce energy consumption. The project team learned, however, that if OA were to exceed 10% of total airflow, exhaust-heat recovery would be required. This would substantially increase costs, making the economizers an unattractive option.
CONFIGURATION
Air handler configurations with various components are shown in Figure 1. Table A indicates air temperatures at various locations within the system and variations by season for Dublin.
Heat recovery: Twelve row coils at 14 fi ns per inch were required to meet the 68% heat-recovery effectiveness mandated by the EU Ecodesign directive. A 30% propylene glycol system was modeled with a flow rate high enough to prevent frosting on the exhaust-heat-recovery coil. Both the power required to drive air through these deep coils and the high glycol flow rate increased energy consumption.
Cleanroom space: The suite was assumed to have a total volume of 2,303 cubic meters (m3), with 25 air changes per hour (ACH) for an ISO 8 space. (This rate is from a previous project where the design was affected by these regulations. ISPE guidelines recommend a minimum of 20 ACH for a classified space.) The main suite is 2,200 m3, with the remainder of the space split among three airlocks/gowning rooms. Total airflow for the system is 16,000 liters per second. Fan efficiencies were assumed at a high 75% to ensure that fan heat was low. The supply fan has a static pressure of 1,250 pascals (Pa), and the return fan has a static pressure of 747 Pa. Heat-recovery fans were sized for 528 Pa combined. Internal lighting loading was assumed at 10 watts (W) per square meter (m2) and 5 W/m2 for general loading. Internal loading was intentionally kept low to show the ineffectiveness of exhaust-air heat recovery, even in systems with low heat loads. The space was analyzed with no outside walls, which is typical for cleanroom locations.
Utility: The utility space was assumed to have the same area, volume, fan efficiencies, and internal heat loads as the clean space. Airflow was set to just meet system needs. Supply fan was analyzed with a static pressure of 1,000 Pa, and the return fan at 650 Pa. Heat-recovery fans were 528 Pa combined. The area served was assumed to be square, with 50% of each side along an outside wall, and with 20% of the wall comprised of windows. Insulation and window solar-heat-gain coefficients were assumed to be 80% of ASHRAE 90.1 version 2013 (3)–compliant values to ensure that the values were not understated. The air-change rate ranged from 5.3 to 6 ACH, depending on location.
System | Athens, Greece | Dublin, Ireland | Helsinki, Finland | Wynau, Switzerland |
||||
---|---|---|---|---|---|---|---|---|
ISO 8 | Utility | ISO 8 | Utility | ISO 8 | Utility | ISO 8 | Utility | |
When OA% is below | ||||||||
Base has a lower carbon footprint than the runaround loop with bypass |
< 20% | < 51% | <20% | < 45% | < 12% | < 17% | < 17% | < 32% |
Base has lower carbon footprint than run-around loop without bypass |
< 46% | < 83% | < 27% | < 78% | < 19% | < 26% | < 24% | < 43% |
Economizer has lower carbon footprint than run-around loop with bypass |
< 43% | <70% | < 30% | < 68% | < 21% | <30% | < 26% | < 44% |
ISO 8 space is based on 25 ACH; utility space airfl ow is based on load at 5.3–6 ACH, depending on location |
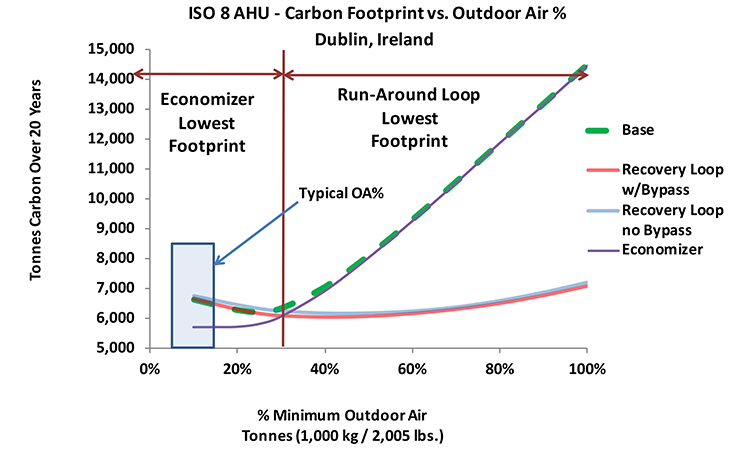
Utility generation and cost: The base analysis assumes that hot water is heated with a natural-gas-fired boiler, with a steam-to-hot-water converter at 77% efficiency, which includes distribution losses on design cooling days, with adjustments made for variations in combustion air temperature throughoutthe year. Energy cost includes both natural gas (to generate steam) and electricity to operate the pump. A more efficient condensing boiler could have been modeled, but it would be unusual for an owner to install condensing boilers to cover the heating load when they already have steam boilers. In the end, more efficient hot water heating would lead to even less value in exhaust-heat-recovery systems since less energy would be saved compared to the steam boiler system.
Chilled water was generated by an electricity-driven plant. Chilled water cost includes chiller, pump, tower fan power, and tower water makeup. Energy consumed to generate chilled water was based on an electric utility cost spreadsheet with a sliding coefficient of performance based on outdoor wet-bulb, load, and cost of tower water make-up. Energy rates were based on Eurostat energy statistics4 for each country. The calculations were run using bin data spreadsheets. These were cross-checked against a Trane Trace7005 modeling program and were found to have similar results.
Figure 2 shows the effect of various utility demands for Dublin at 10% OA for the ISO 8 space. All data below €35,000 is base unit supply and return fan power, and is equal for all options. The difference in fan energy cost is associated with heat recovery; heat recovery with no bypass had the highest fan power. The chart shows that the heating energy cost for all four options—reheating air after dehumidification in summer—are the same at €4,140. The biggest difference in energy cost is the lower cooling load using an air-side economizer; this takes advantage of the cooler OA available most of the year. The difference is significant and is the main contributor to energy cost savings, which correlates closely with energy consumption and carbon footprint.
None of the four locations showed a winter heating load for either the clean space or utility space air-handling system at 10% OA. Recovering heat in the exhaust stream doesn’t appear to be useful for reducing energy consumption due to internal heat loads and/or high air-change rates.
Figure 3 shows the carbon footprint over a 20-year life cycle for the Dublin ISO 8 clean space air-handling systems. Note that the economizer unit has the lowest carbon footprint when minimum OA is below 30%. In addition, there is little difference between the units with exhaust heat recovery and the base approach below 30% OA. This is attributed to internal heat generation within the facility so that mixed air does not require additional heat to satisfy space conditions.
Results
The cost of operating with heat recovery—with or without air-side bypass—is higher than the base unit without heat recovery at lower OA rates. This is partly because heat recovery is not usually needed, and when heat recovery does operate in peak summer design periods, it provides minimal free cooling, since OA is at 25 ̊C and exhaust air is at 20.8 ̊C for clean space unit and 22.7 ̊C for the utility unit. The cost to run the heat-recovery pump and fans is greater than the electricity and tower water savings from a slightly lower chilled-water load.
The largest savings are derived from the free cooling provided by the air-side economizer, a method not recognized by Swiss or EU energy code regulations. ASHRAE 90.1 requires an economizer for most climate zones in addition to heat recovery above 10% OA.
Figure 4 shows the carbon footprint over a 20-year life cycle for systems serving a utility space. Note that the base and air-side economizer have a lower carbon footprint, even at a higher OA rate relative to the ISO 8 cleanroom analysis. This is due in large part to right-sizing the AHU to just meet load, minimizing the reheat impact and increasing free cooling by lowering air delivery temperatures to meet load at the lower airflow rate. Table B lists the percent of OA below which the base and air-side economizer systems have a lower carbon footprint than the heat-recovery loop, with or without bypass. For the 25 ACH ISO 8 space considered, adding exhaust heat recovery increases energy consumption when OA is below 12%–20%, depending on location. For the utility space, adding exhaust heat recovery increases energy consumption when OA is below 17%–51%, depending on location. If an air-side economizer is added to the base AHU, it reduces energy consumption when OA is below 21%–43% for the ISO 8 space and 30%–70% for the utility space, depending on location. This is a better value than the code-compliant unit with exhaust heat recovery and air-side bypass.
Conclusion
Current energy codes in both Europe and the US are intended to reduce energy consumption and reduce carbon footprint. Depending on the code considered, facilities are either required to have or find it hard to avoid installing exhaust-heat recovery on air-handling systems with 10% or more OA. For clean spaces and supporting mechanical utility spaces, however—those with moderate-to-high heat loads and/or high air-change rates and low OA percentages—the analysis presented here shows that the codes do not appear to reduce energy consumption and carbon footprint as intended.
Figure 4: Utility Ahu, Carbon Footprint Vs. Oa%, Dublin – large image graph
The capital cost of installing code-compliant energy-recovery systems can be significant and includes:
- Additional building footprint and volume
- Increased engineering
- Added equipment
- More complex systems and controls
- Associated test and balance work
These systems also require additional care in design, installation, and commissioning, plus annual maintenance costs such as equipment maintenance, filter replacement, and instrumentation calibration. The added equipment and system complexity may increase the risk of potential system failure. These costs were not factored into the analysis.
As these codes are applied to many HVAC systems used in the pharmaceutical industry, they drive higher energy consumption and greater carbon footprint than would be necessary if an air-side economizer were recognized as an alternative energy-conservation measure for low-to-moderate OA rates, as identified in Table B.
EU regulation 1253/2014 will be reviewed in 2019, and ASHRAE 90.1 comes up for review every three years. These reviews may provide opportunities for the pharmaceutical and other high-tech industries to influence requirements and interpretation of these documents by gathering additional data and ensuring that regulations provide the lower energy consumption and carbon footprint intended.
- 4European Commission. Eurostat. Statistics Explained. “Consumption of Energy.” http://ec.europa.eu/eurostat/statistics-explained/index.php/Consumption_of_energy
- 5Trane. Trace 700, Version 6.3.3.1.S—2016. http://www.trane.com/commercial/north-america/ us/en/products-systems.html