Digital Reference Architecture Principles for Data-Driven Pharma Factory

As members of the Architecture Team of the ISPE Pharma 4.0™ Plug & Produce Initiative, we would like to share the principles we have developed with the broader life sciences community. Our aim is to foster further exchange and dialogue about these principles.
Currently, two dominant obstacles must be overcome to transform data collection, real-time bidirectional data transfer, and data analytics in life sciences manufacturing:
- There is a disconnect between shop-floor activities on the one hand, and decision-making on different enterprise levels on the other.
- Many types of locally run software do not conform to an Industrial Internet of Things (IIoT) standard for the pharmaceutical industry.
With connectivity protocols such as OPC Unied Architecture (UA) and MQ Telemetry Transport (MQTT) in place, many manufacturers in the life sciences sector are already implementing machine-to-information technology (IT) connectivity from the shop-floor level to the enterprise level on a limited basis. However, the broader rollout of connectivity is hindered by shortcomings in integration engineering and qualification. In this article, we propose that digital reference architecture is a simple and feasible solution to this challenge in both brownfield and greenfield scenarios.
Digital Reference Architecture
Figure 1 maps the transition from the current (legacy) world with its closed systems—such as distributed control systems (DCS), supervisory control and data acquisition (SCADA) systems, manufacturing execution systems (MES), and process historian and analytics tools—into a future in which service-oriented data reference architecture is characterized by the following three main attributes:
- Supplier equipment (e.g., package units, supply units, sensors, portable appliance tester equipment) “speaks” the same language as IT services and functions.
- Message-based publication/subscription (“pub/sub”) is used instead of tag-by-tag integration engineering.
- Enterprise-level pub/sub is used for service-to-service communication.
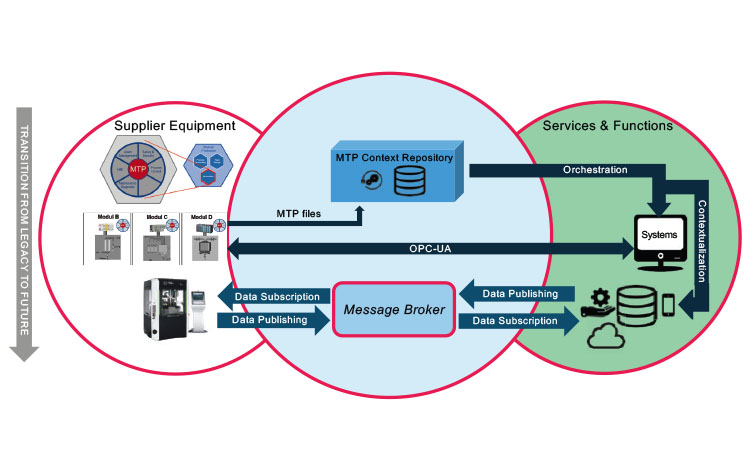
Unifying the Languages of Supplier Equipment and It Services/Functions
The NAMUR Module Type Package (MTP) presents a possible standard for the formal representation of equipment capabilities. Under this standard, the MTP file incorporates a full data interface specification to completely describe equipment data semantics. Bidirectional connectivity of process data (continuous and alarms/events), user data, and time sync allow for machine-to-machine interaction through process orchestration services. Equipment suppliers provide life-cycle management for the MTP file for the life of the delivered machines as part of a service-level agreement with the user, ensuring that the user receives all modifications or upgrades made to the MTP file. Thus, suppliers can systematically bring innovation (e.g., additional inline sensors, smart-equipment functions) to their established customer base. This paves the way for new business models such as software as a service (SaaS) or equipment as a service (EaaS) in the supplier market.
In this model, the MTP files are under strict version control; for example, they could be maintained in an MTP repository on the users’ side. The various services subscribe to the MTP repository and are thus aware of the equipment capabilities currently present on the shop floor. These services can include:
- Process orchestration
- Data storage/archiving
- Dashboards
- Decision aids and workforce support (e.g., remote operator guidance or operating guidance via smart devices)
- Predictions related to manufacturing operations (e.g., main maintenance “sweet spots”)
- Operations optimization (e.g., improvements in overall equipment effectiveness)
- External data exchanges (e.g., with regulators, partners, or suppliers)
Once a service’s interface configuration complements a managed MTP le, connection consistency is ensured without any human interaction. There is no need to translate equipment data for a particular service (i.e., no need for integration engineering) because complete equipment data semantics are available with the MTP file.
Using Message-Based Pub/Sub Instead of Tag-By-Tag Integration Engineering
By default, if data reference architecture is used, equipment and services publish all of their data via the “message broker” in real time (see Figure 1). The message broker is a neutral component, unaware of the message structures and content. Its main functions are the distribution, buffering, and secure transfer of data. Data manipulation is constrained by policies and is subject to a full audit trail. Point-to-point and tag-by-tag engineering and qualification are not required. This saves precious time-to-production and integration engineering costs.
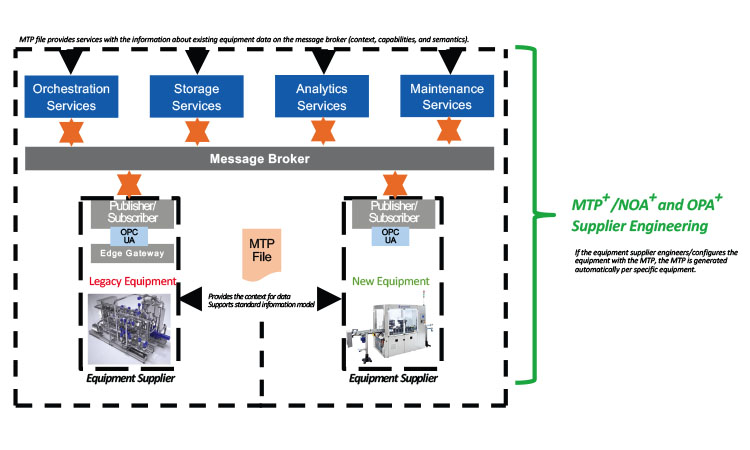
Using Enterprise-Level Pub/Sub for Service-To- Service Communication
Service-to-service communication is also achieved via a message broker, in the same manner as described previously. Services publish information and can subscribe to other services’ data. The need for point-to-point connections between IT systems vanishes. The use of enterprise-level message brokerage (which is also referred to as “message-oriented middleware” or an “enterprise service bus”) is a broadly accepted best practice for the flexible and maintainable integration of IT systems. Other regulated and data-integrity–sensitive sectors such as the financial industry are already using this type of message brokerage. Such solutions provide scalable, secure, and cost-efficient low-latency exchange of data.
Implementation Options
The three main attributes of data reference architecture described previously can be realized with today’s connectivity and IT technologies. In addition to NAMUR’s standardization work related to MTP and open architecture (NOA), the life sciences industry should consider the concepts and implementations developed around the Open Group’s Open Process Automation (OPA). To create the message broker functionality, technical options range from a single “magic” product to a combination of multiple technologies, with the latter being a viable approach during the architectural transition phase.
Figure 2 provides a different perspective on the digital reference architecture presented previously. If MTP is considered the standard, it should become more than an instrument of core process control engineering. It should also be enriched with additional information (e.g., the full scope of the audit trail and system events) as well as a full set of equipment metadata, including unique identifiers, version information, and so on. The MTP should also include security mechanisms (e.g., checksums) and equipment life-cycle details.
The resulting “MTP plus” (MTP+) would offer cost-efficient standardized integration of legacy equipment to users. Furthermore, suppliers who use the MTP+ model for new equipment could streamline their engineering processes and ship the MTP+file with the specific equipment. This would allow suppliers to provide plug-and-produce solutions in the shortest amount of time possible, and users could get equipment up and running much faster through a more unified qualification approach, while almost completely reducing the need for integration engineering.
Similarly, concepts like NOA and OPA could be extended to “NOA+” and “OPA+” to demonstrate that the message-based pub/sub is not just an instrument to transport field-device data to the cloud. These concepts will need to support high-volume, bidirectional data streaming.
Summary and Outlook
The life sciences industry can build on existing best practices and solutions in IT and IIoT to establish digital reference architecture for data-driven pharmaceutical manufacturing.
The idea of an enterprisewide service bus, message broker, or data gateway and systems decoupling is well established. In fact, every smartphone user benefits from highly sophisticated IT/operational technology architecture. For example, your favorite app knows that it can subscribe to a contacts service and automatically asks for this permission upon initial launch. Your smart-home devices from various vendors automatically appear in your home surveillance dashboard once they connect to the wireless network.
In the pharma industry, challenges related to data resource architecture arise from the lingering automation-pyramid mindset, entrenched automation and IT silos, and the lack of consensus about principles and standards. The NAMUR activities around MTP and NOA, the Open Group’s OPA, and the latest version of the International Society of Automation’s Enterprise-Control System Integration (ISA-95) Standard provide the perfect foundation to start real-world projects. These projects will rely heavily on new collaborations between innovative equipment suppliers, cutting-edge IT partners, and open-minded users.
This article and related activities of the Pharma 4.0™ Plug & Produce Initiative are an open call for engagement. The initiative is actively engaging a community of users and suppliers, and it is excited to see a growing number of contributors, proofs of concepts, and projects across the industry.
Additional Resources
Automatisierung modularer Anlagen
https://www.namur.net/fokusthemen/automatisierung-modularer-anlagen
Industry Standards Groups to Converge Their Work
https://www.arcweb.com/blog/industry-standards-groups-converge-their-work
Open Process Automation Update
http://wps1705.international-bc-online.org/wp-content/uploads/2017/09/1.-Forbes-ENG.pdf
ISA-95 evolves to support smart manufacturing and IIoT
https://www.isa.org/intech-plus/2018/feb/isa-95-evolves-to-support-smart-manufacturingand-iiot/
Patterns and Best Practices for Enterprise Integration
https://www.enterpriseintegrationpatterns.com/index.html